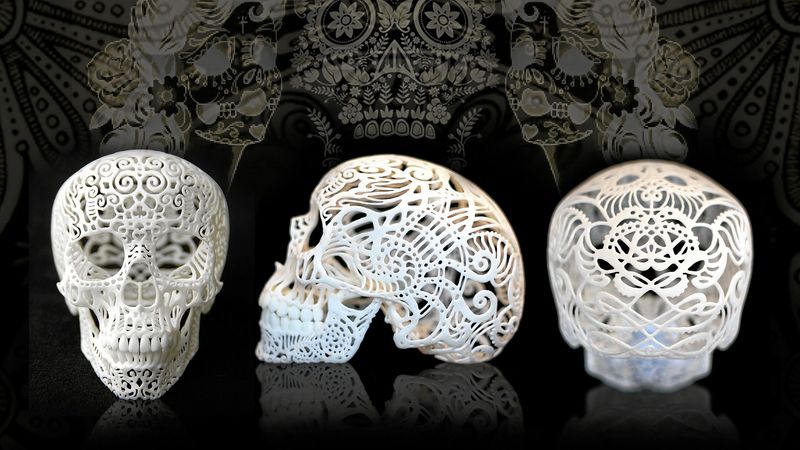
From a distance, it looks like an ordinary human skull, its white surface contrasting with the black velvet it rests on. But, as you move closer, you realise that the cranium fractures into filigree detail, something that its creator, the United States-based sculptor Joshua Harker, says symbolises his attempts to break away from traditional ways of making and disseminating art.
“I was very frustrated,” says Harker. “No one understood the medium. Born out of this frustration, it [the skull] was the death of me committing to this traditional network [of galleries and way of selling my art] and cloud of resources. The filigree is symbolic of this creative exploration and a new way to connect and put art out there using crowd funding and social media.”
Harker shot to international fame in 2011 when, through Kickstarter, he raised more than $77 000 for his sculpture project — Crania Anatomica Filigre: Me to You — in 45 days, although he asked for only $500. He still holds the record for the most amount of money raised for a sculpture using crowd-sourced funding.
Before that, he had struggled to sell his work created by using 3D printing.
“I had this new medium, and galleries didn’t understand it and neither did collectors. It made it difficult to distribute and disseminate [my work],” Harker says, noting with a smirk that he now has to turn galleries away and sells the majority of his work online.
His work is part of more than 3 000 private collections around the world, some of which include artists such as Andy Warhol. At the moment, some of Harker’s work is being exhibited at the London Science Museum and was recently showcased at the Art Basel in Miami Beach.
Harker is one of the artists showing his work at the Agents of the 3D Revolution, a series of lectures, exhibitions and technology demonstrations hosted by the University of Johannesburg’s fine art and architecture department gallery from July 5 to 22. The event is being sponsored by the National Research Foundation and the Vaal University of Technology to create awareness about 3D printing.
The new industrial revolution
Art, in many ways, is pioneering a path that many in the manufacturing industry have not yet realised exists. And that is what the exhibition is about, says Michaella Janse van Vuuren, a Johannesburg-based doctor of electrical engineering who is co-ordinating the exhibition.
“I see this wave of 3D printing coming,” says Van Vuuren, who is also showing some of her own work.
“It’s the new industrial revolution and it’s going to completely change how things are made.”
Digital sculptor Keith Brown, whose work has been shown in galleries around the world, including at the Royal Academy of Arts Summer Exhibitions of 2002, 2003 and 2005, is the founder and president of Fast-UK (Fine Art Science and Technology in the United Kingdom).
Among the work he will be showing at the Johannesburg exhibition will be his piece Dive. It’s a pale mixture of soft curves and sharp edges knotted together, an abstract piece that was first conceived on a computer. Brown calls it “real virtuality” rather than a “virtual reality”.
“We are making manifest concepts that are derived from the virtual environment,” Brown says about 3D printing, which is about taking something from a computer screen and making it a reality rather than the other way around.
Michaelanglo once said that “every block of stone has a statue inside it and it is the task of the sculptor to discover it.” But technology such as 3D printing — otherwise known as rapid prototyping — has turned that approach on its head.
“It’s not just the capability to make a wide range of objects,” says Brown.
“We can make manifest concepts that are derived from the virtual environment and make them manifest in the real world.”
The artist is no longer inhibited by the characteristics of a stone, gravity or a misplaced chisel chip.
“There aren’t any physics in there [the computer modelling program] — you have mathematics, no physics, no weight, no gravity. [You create] visibles of a 3D nature that would be inconceivable in the real world” and then 3D printing lets you realise them, Brown says.
He takes an academic approach, which is unsurprising since he is also director of art and digital technologies at the Manchester Metropolitan University.
“I don’t set myself a brief or problem to solve and then find a design that solves this problem,” Brown says.
“I work through serendipity. I push things around and observe what’s happening, and then something happens that you didn’t expect.”
One of his focuses is on material behaviour, “the idea of appropriateness of materials in sculpture”.
He cites the example of glass and stone dust that he allowed to pass through a sieve and noted the different ways in which it fell depending on how he shook the sieve and how high he held it.
Practical engineering
“The material was behaving in a way that was natural to it. This began to guide me in my work. To me, it’s a question of it’s so because it is so, rather than I say so. There’s anonymity in the work [because] I don’t have anything to say. It is about my explorations and finding things that I consider amazing and wonderful,” he says.
Other artists choose 3D printing because of the versatility of the medium.
Van Vuuren’s works on display are dreams of childlike fantasy and practical engineering. One of her best-known pieces is her Horse Marionette, a winged horse puppet that dances and cavorts in any way the puppet master wants it to, highlighting the versatility of the medium.
“I designed it on the computer, sent it to the printers … it was made all in one go, joints and all,” she says.
“That is what amazes me about 3D printing … you shake the powder loose [once the printing is complete] and it moves!”
Meanwhile, the Scottish artist Geoffrey Mann, whose work has been shown at MoMA New York, is showing Blown, one of his best-known series. It is a collection of teacups, each unique but following the same pattern. In the video explaining the series, a person blows on a cup of tea and the ripples scatter across the surface of the liquid; then the cup itself vibrates as though someone is blowing on it, behaving like a liquid.
Mann has managed, using computer algorithms and 3D printing, to recreate this “blown upon” teacup, integrating “traditional and digital practices and, in doing so, creates a craft that is more dynamic”.
He has developed an app, called Blown, that can be downloaded from iTunes and allows users to blow on to their screen and interact with a teacup in real time and upload it to Twitter.
“The app will be the first of a series that will allow the user to interact with the studio process,” he says.
Although digital printing expands many artists’ horizons in terms of what is possible, it also brings inherent dangers, such as how to protect your work and copyright it. Brown says that since his work is contained in a digital file, it is possible to send that file to a 3D printer in a different country to be created.
“One of the odd things is when you send a file across the world to Australia or New Zealand or the [United] States and they print it for you. On occasions, you don’t get to see the object. It’s strange making a work that you might never see,” he says.
Harker dismisses the idea of selling files of his work, although he says he has been approached by companies wanting to do that.
“The problem is piracy. [The file containing the art] goes out there, and there’s no way to support yourself from your work when it’s all free.”
Moulds are so yesterday
Three-dimensional (3D) printing, otherwise known as rapid prototyping or additive manufacturing, is a global phenomenon. With this technology, you can create any physical model, no matter how intricate, and even with moving parts, from a software file sent to a printer from anywhere in the world.
On a large scale, it is being used to manufacture hi-tech specialised parts for the aviation industry and custom-made biomedical prostheses such as hip joints.
On a smaller scale, there are examples like the one of South African Richard van As, who in 2001 lost four fingers in a woodworking accident and used 3D printing to build himself a new hand, called “Robohand”.
The technology has since been used to rebuild a hand for a five-year-old boy who lost his fingers because of amniotic band syndrome — they were caught in part of the amniotic band in his mother’s uterus.
3D printing works by building up an object layer by layer. Granules of a material — which can be a variety of substances, including plastic and metal — are spread on a surface and welded together using a laser.
Once the first layer has been melted, more granules are sprinkled on top and they are welded to each other and the layer below. These layers are incredibly thin and allow a degree of precision and detail impossible with previous technology.
For example, it is possible to build a collection of Russian dolls, each packed one inside the other, without opening the outer doll.
Also, you can make one object at a time to incredibly accurate specifications, so it is ideal for prototyping.
South Africa, through a collaboration with the Council for Scientific and Industrial Research and the South African aircraft parts manufacturer Aerosud, is building the world’s fastest 3D printer.
The project is focused on the aviation industry because, to build an aircraft, you need a small number of highly specialised parts. Older forms of manufacturing technology, such as machining or injection moulding, make the parts very expensive because valuable raw materials, such as titanium, are wasted in the production process.
Rapid prototyping means that manufacturers — and artists — can make once-off, customised items without making a mould. These can also be made on order so manufacturers don’t have to put out capital upfront for products they might not be able to sell.
For more details about Agents of the 3D Revolution, on from July 5 to 22 at the University of Johannesburg, go to agentsofthe3drevolution.com