It surrounds us. We’re housed in it, we work in it, we travel on it. Cement is the most overlooked of construction materials.
Some reports would have us believe that after water it is the second mostused substance on the planet. What is an accepted fact regarding cement, however, is the product’s extremely high carbon footprint.
The cement industry is responsible for about 5% of the world’s carbon dioxide (CO2) emissions, the gas most responsible for global warming. But as the world continues to develop and economies expand, the demand for cement is unlikely to wane.
It is not an easy product to recycle and it is exceptionally energy-intensive to produce. It requires large amounts of fossil fuel, usually coal, to fire the kilns used in the manufacturing process — the combustion of which itself releases CO2.
A kiln needs to burn at thousands of degrees Celsius to break down limestone, the raw mineral used in the manufacturing process.
A by-product is CO2, which further adds to the emissions output. In South Africa the cement industry is believed to account for about 1.67% of CO2 emissions, although this is heavily diluted by other industries such as Sasol, Eskom and the steel industry. ‘This is not a comforting figure for us,†said Alan Cluett, environmental manager for the local cement manufacturer, Afrisam.
As such, the company has introduced an environmentally friendly mark on its products, which indicates each cement type’s relative carbon footprint. The world emissions average of CO2 per kilogram of cement is 890g. Afrisam’s products will carry a thermometer insignia showing the relevant CO2 output compared with the world average.
But how can a product, which releases 60% of its CO2 in the decarbonisation of limestone and 40% from burning fuels, become greener?
By its very nature an inevitable by-product of cement manufacture is CO2. According to Stephan Olivier, chief operating officer for cement operations at Afrisam, the breakdown of energy sources in the production process is roughly 87% from coal consumption, 11% from electricity consumption and 2% from diesel consumption.
The milling of raw materials, kiln firing and cement milling are the most energy-intensive parts of the process. But through a range of steps the company has been able to increase energy efficiency. These include kiln upgrades, making them more fuel efficient, as well as the use of cement extenders to reduce CO2 output.
Cement extenders mean less clinker content is required. Clinker is the raw material created during the kiln firing process and it is part of the final cement product.
Extenders include slagment, silica fume, fly ash and limestone. Not only is less CO2 produced with the addition of extenders, but also less energy is used in the process. With the use of extenders, such as slagment, electricity consumption during manufacturing can be halved, said Olivier.
Slagment is a binding material, similar to cement, and can replace up to 70% of cement content in concrete. The use of fly ash — a by-product of steel manufacturing — requires 95% less electricity, according to Olivier.
In recent years, said Olivier, Afrisam decreased its electricity consumption from 123kWh a ton of cement to about 90kWh a ton of cement. Similarly, the thermal energy consumption decreased from 3.8megajoules (MJ) a ton of cement produced to 2.2MJ/ton.
Products such as Afrisam’s all purpose cement, manufactured at the company’s Roodepoort plant, will produce 527g of CO2 a kilogram of cement against the world average of 890g/kilogram.
Ultimately, the use of greener cement will depend on the uptake by customers. Consumers from large construction firms on state projects down to small building companies will have to buy greener products.
In addition, the chances of the industry becoming carbon neutral are slim. The global industry has long been attempting to go green.
As far back as 1999, under the auspices of the World Business Council for Sustainable Development, 10 leading cement companies commissioned independent research into how the industry could address the problems of sustainable development.
Today the result is the Cement Sustainability Initiative, which includes the 18 largest manufacturers of cement in the world, which account for 30% of global cement production, all committed to reducing cement’s carbon footprint.
But although the industry is working towards becoming more energy efficient and less CO2 intensive, innovative young companies are attempting to create entirely green cements. Last year British-based Novacem introduced a new cement based on magnesium silicates.
The product not only requires much less heating, it also absorbs large amounts of CO2 as it hardens, making it carbon negative, according to a report in The Guardian newspaper.
The company has already garnered interest from the British government as well as from large firms such as Rio Tinto. How viable it will be and how quickly the human race can wean itself off its reliance on cement, however, remains to be seen.
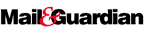