The McLaren factory is all sleek lines and glass. Graeme Robertson/Guardian News & Media Ltd
Secretive billionaires, princes and superstars might supply the Formula One circuit with its brash glamour and pageantry but when the season returned with a roar in March, two of the cars tearing round Melbourne's Albert Park had been constructed in a sleepy corner of Surrey.
The McLaren technology centre (MTC) in Woking exemplifies the quieter fortune being made by the United Kingdom (UK) motor sport industry: the Norman Foster-designed building is the centrepiece of a sector worth around £6-billion to the UK economy. Eight of the dozen F1 teams who competed in last year's championship are based in the UK, and McLaren, which came third in the constructor's league, is one of its most successful participants.
At McLaren's headquarters, the relentless pressure of the F1 calendar is distilled to a zen-like focus. Long white corridors and glass lifts take visitors to an indoor boulevard: historic McLaren vehicles are lined up on one side, and an artificial lake can be glimpsed through a glass wall on the other.
Ron Dennis, executive chairman of the group, which is majority owned by Bahrain's sovereign wealth fund, describes the atmosphere as "a reassuring hush". The new racing car was built behind frosted glass at one end of the boulevard. But McLaren is looking beyond motor sport: in 2011 it opened a production centre next door, where it builds the 12C and 12C Spider sports cars — offshoots of decades of competing in the upper echelons of F1.
Production of the £200 000 12C model is overseen by Mike Flewitt, who managed production of 8 500 vehicles a day when he was vice-president of manufacturing at Ford of Europe. McLaren produced a total of 1 552 cars in the whole of 2011.
"We are a road car company that has developed from a race car company," he says. "This is McLaren standards applied to state-of-the-art vehicle manufacture."
At Ford, Flewitt operated to a cycle time — the time taken by a production line task — of 45 seconds.
At McLaren it is 45 minutes. There is no conveyor belt, no noise from stamping machines or robots. The only sound is the squeak of tyres as completed models are driven across the white-tiled floor into testing booths.
Flewitt says: "If you have a white floor, it creates an imperative to keep it clean. It looks like this because we want it to be a great working environment. I also believe the aesthetic is vital. This gives you confidence in the quality of the product. It is difficult to give people that confidence if you work in a tatty facility."
In contrast with mass-market manufacturers, the paint finish is applied manually by specialist staff rather than by robots. I watch Flewitt submit a finished 12C Spider bound for Singapore to a minute inspection.
He praises the way the volcano-orange paint has been sprayed on to the contoured vehicle. "Paints have different compositions," he says. "The sprayer's art is to understand the model so you get an even finish."
There would be no financial or aesthetic gain from spending millions of pounds on paint-spraying robots, he adds, instinctively flicking away a dust mote. Like their mass-produced counterparts, the majority — eight out of 10 — of McLaren sports cars will be exported. Four dealerships opened in China last year.
Elsewhere in the building are other examples of McLaren excellence, overseen by its McLaren applied technologies (MAT) arm, which supported Team GB in cycling, canoeing, rowing, kayaking and sailing at the 2012 Olympics.
The rationale behind MAT is that McLaren should make more financial gain from its world-class abilities in design, analysis and production. At one end of the boulevard, propped next to an F1 car, is the £25 000 Specialized S-Works Venge bike ridden by Mark Cavendish in the 2011 Tour de France, which McLaren helped design.
The director of MAT, Geoff McGrath, says McLaren's skills in telemetry — monitoring a car's performance through accumulated data — are the key. This allows McLaren to simulate how a car, or any product, will perform by building a computer model of it.
McGrath says: "We took a formula that worked very nicely for racing car design, then applied it to road car design, then bike design. We take the knowhow, the skills that we never commercialised, and hundreds of millions of pounds of research, and apply it to new markets."
The healthcare market is the company's next target, he says. The British automotive industry has delivered a strong performance in the post-crunch doldrums. But although Nissan added a further 280 jobs at its plant in Sunderland in November 2012, carmakers are unlikely to open new sites in the UK; what is more probable is that they will follow the example of Jaguar Land Rover, which recently started work on a factory in China. The hope is that suppliers — the makers of nuts, bolts and components — can spur domestic growth in the UK.
There is an estimated £3-billion worth of unsatisfied demand for UK-made components.
Nick Henry of consultancy ICF GHK says Britain's F1 industry has dominated the sport for more than 30 years despite attempts to develop rival hubs in Bahrain, Malaysia and South Africa: "The history of F1 is continued UK success in the face of globalisation, which is chipping away at it but feeding its growth at the same time.
"These are flexible small and medium-sized businesses doing high-quality engineering.
"There has been churn in [team] ownership but behind it this core of British engineering creates products the world pays for."
Amid the clamour over the need to rebalance Britain's struggling economy, the long-term success of the UK's motor sport industry offers a quiet lesson in how it can be done. — © Guardian 2012
Although this article has been made possible by the Mail & Guardian's advertisers, content and photographs were sourced independently by the M&G supplements editorial team. It forms part of a larger supplement.
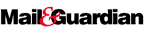