In addition to Bio2Watt's Bronkhorstspruit plant
You cannot help but notice the smell. It hangs over the cattle in their feeding lots, a heavy pungency permeating the air.
In the distance, large steel cylinders, some topped by metal domes, rise above the animals – decidedly out of kilter with the mud and manure, and the cattle making it.
But the Bronkhorstspruit biogas plant has a unique and very apt place in the landscape, taking up the waste produced by tens of thousands of cattle, and that of nearby industries, and turning it into electricity.
The plant, which began producing electricity on October 10, is the culmination of years of work by entrepreneur Sean Thomas of Bio2Watt.
It is testament to the commitment needed by independent power producers, as well as the funders and other partners working with them to get a project like this off the ground. As Thomas explained to journalists, in a tent ventilated by strategically placed fans, when he began setting up the biogas plant in 2007, it seemed a “no brainer”. The country was running out of electricity and heading into a “perfect storm”. At the same time, public awareness about the “green agenda” was high.
“As an engineer, I wrongly assumed that here you have a proven technology, [and] a perfect storm, so there is no reason for this project not to happen as quickly as possible.”
But the challenges of negotiating the regulatory requirements and environmental licensing needed to get the plant operational was not something he expected. It was eight years later, after he had sunk his retirement money into the project and put his house up as collateral, that the plant was able to begin feeding electricity into the grid.
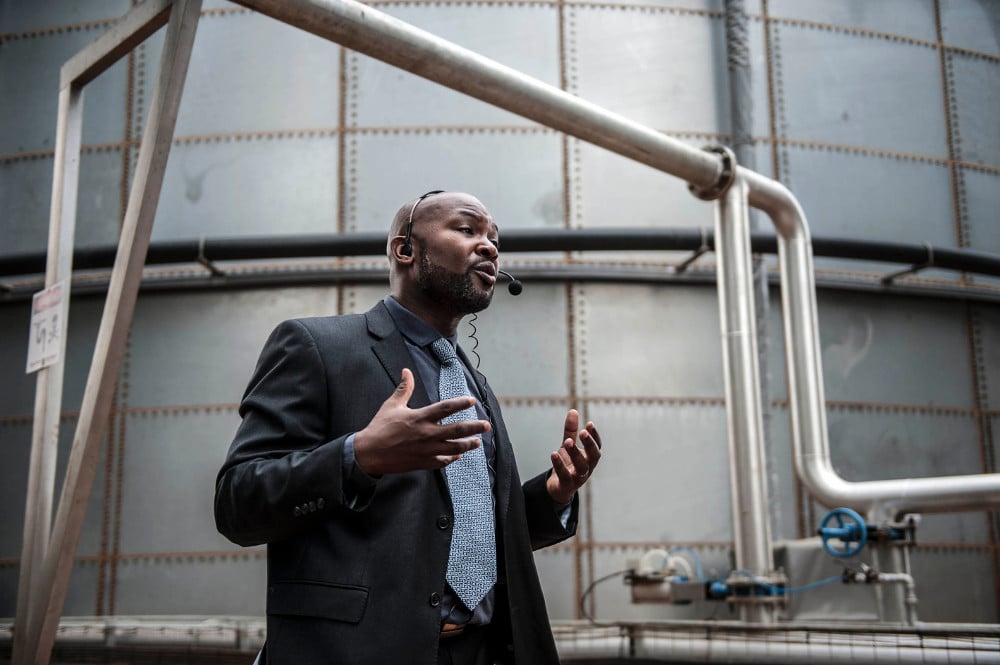
Sean Thomas didn’t think that using proven technology to meet energy needs would be such a headache. (Photos: Paul Botes, M&G)
But persistence has paid off. The electricity the biogas plant produces is destined for vehicle manufacturer BMW, and specifically for its Rosslyn factory north of Pretoria.
It is the first private deal of its kind in South Africa – an independent power producer selling electricity directly to a customer, rather than to the state-owned utility Eskom.
The fact that the electricity has to be transported from the biogas plant to the car maker through grid networks owned by both Eskom and the City of Tshwane – known as “wheeling” – contributed to the delays. The city had no wheeling agreement in place when the project began and it was one of the many agreements that needed to be negotiated.
But now that it is up and running, the Bronkhorstspruit project is being used as a blueprint for similar projects, according to Thomas.
The electricity that BMW will get from the biogas project is part of the company’s effort to eventually source all the power it uses in its production process from renewable energy sources. The Rosslyn factory will get 25% to 30% of its energy needs from the biogas plant, and has signed a power purchase agreement with it for the next 10 years.
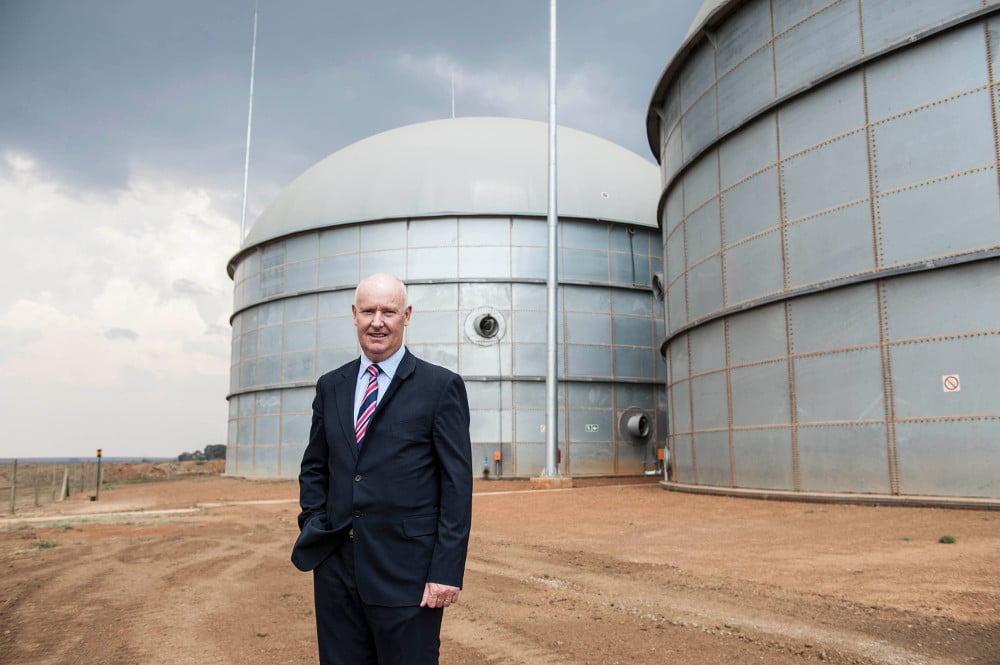
BMW South Africa, headed up by Tim Abbot, bought into Thomas’s dreams.
The managing director for BMW South Africa, Tim Abbot, said that although there were delays, supporting the project was “the obvious way to go”. The company’s decision was driven by environmental sustainability rather than solely by cost, he said.
“We have yet to see the full effects of a price reduction. It’s more about sustainability than the cost,” he said “But obviously, as a prerequisite, we wouldn’t want it to be more expensive that what it [currently] costs.”
He added that, with the threat of load-shedding, the power from the biogas station brings consistency and stability to the Rosslyn plant.
Although Thomas did not give a price for the electricity produced, he said the work done in engineering the biogas plant to fit its current conditions enables it to produce electricity at around current “utility” prices.
According to Eskom’s most recent annual report, the cost of electricity for the 2014-2015 financial year is about 61c per kilowatt hour.
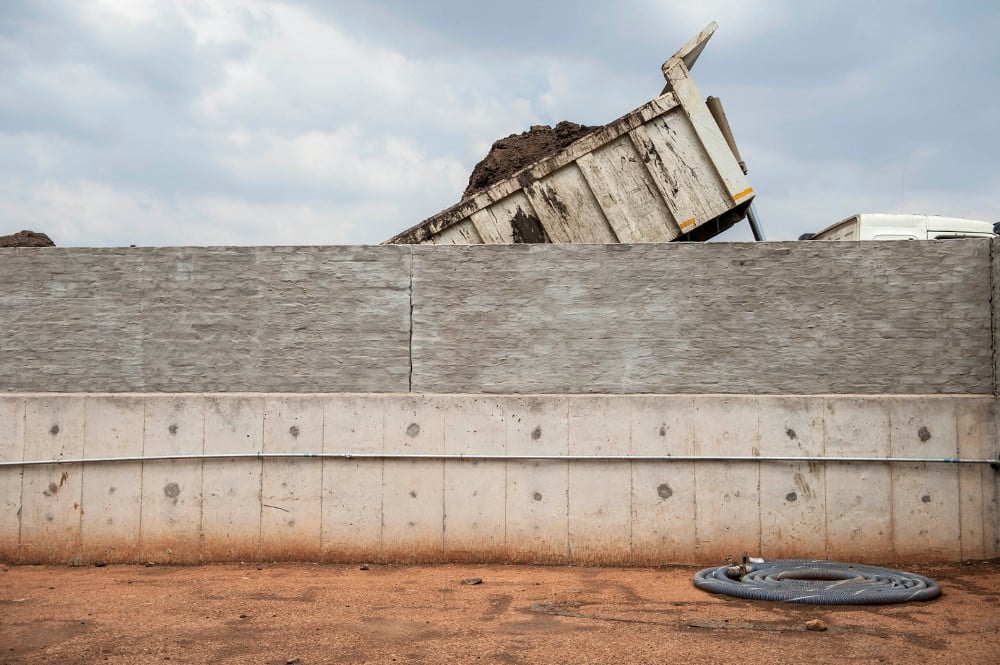
Manure sourced from cattle feedlots is off-loaded at the Bronkhorstspruit biogas plant.
The plant cost R150-million to build and was backed by funders such as the Norwegian state development fund, Norfund, the Industrial Development Corporation, the department of trade and industry (which made a R16-million grant), and the impact funds from two high net worth individuals.
The technology addresses South Africa’s power scarcity and diverts waste from landfills and creates jobs.
Thomas said the project has created about 10 direct and indirect jobs per megawatt, which is higher than other renewable projects, whose job creation rates are about 0.8 to 0.9 jobs per megawatt.
“Because of … the amount of biomass available, the [potential for] replication in rural areas [and] in medium-sized towns, is huge in terms of green jobs,” Thomas said.
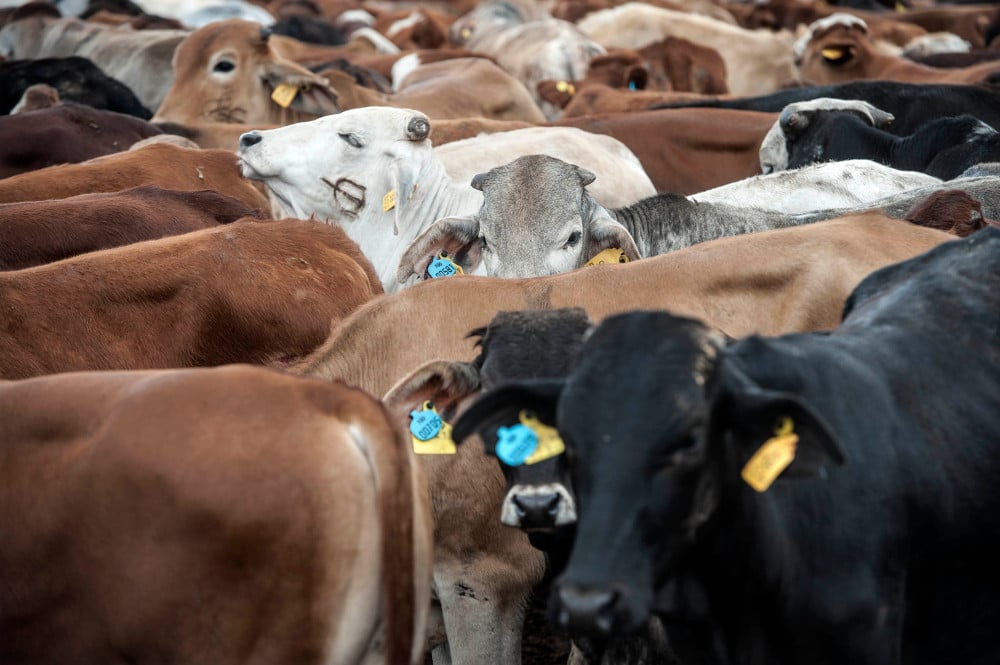
The plant uses manure and other organic matter to produce electricity.
Bio2Watt is planning a second plant at a dairy near Malmesbury. It will submit a bid to the department of energy’s renewable energy independent power producers procurement programme next month.
If successful, it will sell the power to Eskom. But if it is not, Bio2Watt will further discussions that it has had with an industrial off-taker in the area.
The project will also examine waste streams in the catchment around Malmesbury, Paarl and northern Cape Town for use in the plant.
From manure to megawatts
The Bronkhorstspruit biogas plant is located on the premises of one of the country’s largest feedlots, owned by Beefcor.
The plant uses the manure from the feedlot and other organic matter, including abattoir waste and paper sludge, from industries in and around Johannesburg and Pretoria to produce electricity.
The water required for the process is obtained from “pollution dams” on the farm.
The waste is fed into two large primary biodigesters where it is broken down at a relatively high temperature of about 52˚C.
About 80% of the biogas is harvested from the primary digesters, after which the waste is moved to the secondary digesters, where the remaining 20% is extracted.
The gas is stored in large domes over the secondary digesters, which can provide about six hours of supply for the 4.4 megawatt plant.
The fuel is used in gas engines to produce electricity, which is fed into the grid and wheeled to the Rosslyn car manufacturing plant. The power station will use about 60 000 tonnes of organic waste a day.
According to Sean Thomas of Bio2Watt, the operation is already producing more gas that expected, and has to flare between 2.5 to 3 megawatts of excess gas. But the plant has been designed in a way that will it allow it to expand and provide more power in the future.
The methane contained in the biogas acts as the primary fuel to run the gas engines. The gas being produced has a methane content of between 62% and 64%.
Although manure makes up the bulk of the feedstock for the digesters, the gas yields from it are comparatively low. Other waste, such as that from abattoirs, typically gives a greater gas yield, Thomas said.
The global leader in biogas production is Germany, which operates about 10 000 plants and produces 80 gigawatt hours of energy, according to a report by the International Gas Union.
Biogas can also be used to power vehicles.