The old Nokia 2010 came with a range of covers
He’s less than a year old, doesn’t talk yet and is learning to identify, grasp, sort and move objects around. He’s not human, though. “He” is a new baby that has emerged from Seiko-Epson’s research and design facility in Toyoshina, in central Japan’s picturesque Nagano region.
The Autonomous Dual-arm Robot – the acronym is Adar, so let’s call him Adam – is referred to simply as the Epson Robot, but the temptation to name him is irresistible. His face is a stereo camera with a tilt mechanism, but he also has a hand-eye camera in his hands. This allows for 3D object recognition, obstacle avoidance and visual inspection. All features that make him a great asset on the factory floor.
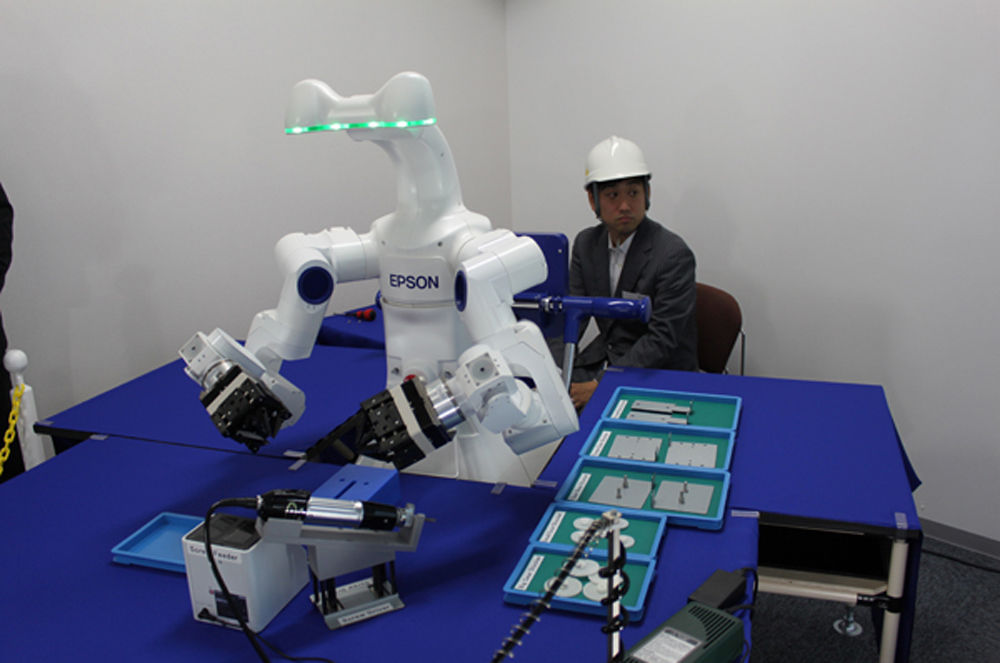
An operator starts up the Epson Robot prototype at a research facility in Nagano, Japan. (Arthur Goldstuck)
That is where Adam is ultimately headed, once testing and development – and safety features – get him to a point where he can work alongside human beings. He looks benign, but you wouldn’t want to discover what 150kg feels like on your foot, or get in the way of his seven-axis arms.
Unlike most current industrial robots, Adam doesn’t have to be bolted into place or anchored, can be moved around easily and can work with a variety of general-purpose tools that he quickly learns to use. It’s not just a nice-to-have for Epson.
“We intend to change the world of manufacturing,” said the company’s global president, Minoru Usui, in an interview in Nagano last week. “Based on our production expertise, we now have industrial robots that are world leaders.
“In 10 to 20 years, I see a world where people are released from manual work to concentrate on work that demands human intelligence. We will solve issues like labour shortages, skills shortages and dangerous working conditions.”
‘Sho Sho Sei’ vision
Epson invested $160-million in its production lines in 2103, and expects to invest a further $100-million this year, in pursuit of its “Sho Sho Sei” vision, Japanese shorthand for “compact, energy-saving, high-precision”.
Meanwhile, the company is expecting a boom in the market for “compact robots” used on assembly lines, comprising six-axis robots and a category called Scara, for Selective Compliance Assembly Robot Arm. From a $580-million market in 2012, it’s expected to rise to $780-million by 2016.
Tsuyoshi Kitahara, chief operating officer of the company’s Industrial Solutions division, says there are two main drivers of the growth in demand for such robots. “Manufacturing is returning to developed economies as labour costs and difficulty in acquiring labour rises in emerging economies. We have also seen an increase in high-mix, low-volume production and shortened product life spans.”
Epson launched the first precision assembly Scara robot in 1983 and now has 30 000 installed throughout the world, giving it a 31% global market share. But it has numerous competitors and it will take the likes of Adam to maintain its leadership. It entered the six-axis robot market only recently and has a mere 4% market share, but that is an indication of its opportunity rather than weakness.
According to Kitahara, the company intends to evolve its offering in the medium term from the current basic robots to high-value solutions for advanced automation, using pressure sensing, for example, to handle fresh food. In the longer term, it will develop “next-generation robotic solutions”, which he sums up as “autonomous working robots that see, sense and think”.
The think part is not about sentient robots, but rather the ability to “decide” what components and tools are needed for an operation, or what path to take to avoid objects. It will then be able to react by itself and work autonomously.
The future of this technology, says Usui, is not confined to the production line, but will become part of assistive care and enhancing the lives of ordinary people. It does not hurt that it looks good in the process. – Gadget.co.za
Arthur Goldstuck is the founder of World Wide Worx and editor-in-chief of Gadget.co.za. Follow him on Twitter on @art2gee.